How can I monitor my refrigerator temperature remotely?
- Travis
- Feb 15, 2022
- 4 min read
Updated: Apr 26, 2024
There are many options to remotely monitor your refrigerator. Some offer more features than others but they all give you the information that you need just in case the temperature is not right in your cooler or freezer. The vast majority of service calls that we get are for a unit being too warm, but on occasion it can also be too cold so a monitor that warns you about both eventualities works best for everyone. In some larger situations someone may also want to know more about temperatures in different parts of the walk-in or the humidity if that is an important element to what is being stored.
Remote monitoring of your walk-in can be as informative as you want ranging from an alarm that sounds when it is above its set point to logging temperature and graphing data. I’ll go over some of the options below. Some are remote and some are there to alert you while you are at the location. Unless you have people onsite 24 hours, units that are not remote may not be the best option but we’ll talk about them anyway because they do alert you to a problem.
The simplest non-remote monitor is one that isn’t remote and for some walk-in coolers is built into the unit’s temperature display with the light switch on your walk-in. This unit, found normally by the door, can be programmed to sound an alarm if the temperature rises above a certain set point. Along with setting the temperature alarm set point you can also program it to set off the alarm after a delay. This will prevent the alarm from sounding every time you receive new product when door is propped open for 20 minutes while they load everything in. This is a cost effective way to have a simple alarm on site that is sleek and part of an already existing system. This kind of temperature display alarm can be added by replacing your existing digital temperature display and easily programmed for your needs. Below you’ll find an image of this type of temperature display/alarm and probe.

Another simple non-remote option if you have staff onsite 24 hours is a dead simple temperature alarm. This alarm has no frills and when it comes down to quick and dirty installations, a technician can be in and out in an hour. This has a big satisfying dial on the front that you set to the temperature you want the alarm to go off at. Below that it has two switches. One is to alarm if the temperature goes above/below the set point and the other is to add a one hour delay to the alarm. It’s as simple as that and many people opt for this alarm because of its affordability and quick set-up. Below is an image of a dead simple temperature alarm.
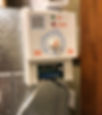
Neither of the two temperature alarms above help you if no one is there to watch over the temperatures. Do you have large walk-ins? Is the temperature in the units critical? This is where remote monitoring comes in and there are a few options for this depending on how much information you need.
The first option is a wifi connected unit that emails you when the temperature gets too high or too low. All it requires is a wifi connection and an app on your phone to set up. It does not provide any graphed data and cannot be programmed to do anything except to let you know when the setpoint has been passed via email. It is an inexpensive option but is fairly limited. If you have one walk-in and want to know if it has gone down remotely this will get you the info you need to get someone out to check on it. Below is an image of the wifi device and its thermistor.
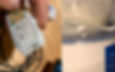
The next system is a smarter version of the above wifi unit that will send you only an email alert. It is a wifi connected unit that offers limited graphing and can email or text when there is a temperature issue. It can significantly help to reduce outages involving temperature. Among the options that we typically offer, it is the Goldilocks solution that gives most people what they need to prevent issues without getting involved with the full monitoring system. Installation is quick and set-up is easy.
The last option is a system designed to watch over multiple units linked through a single base station. It uses a base station and a remote monitoring stations. The base station is connected via direct network cable or wifi to the internet and acts as a gateway for the remote monitoring stations that are placed in coolers and freezers around the facility. Using a wired thermistor probe, the remote monitoring stations send data wirelessly every 60 seconds to the base station which relays that to a server where the data is stored so it can be graphed and viewed. That information is accessible to the customer through a secure website 24/7 and has endless ways that it can display that information and alert you to multiple issues. This type of system can have multiple monitors per walk-in to verify that the temperatures are even throughout the box or to see how a coil is cycling on an evaporator. On a large refrigeration system with an allusive problem, this type of monitoring allows the customer and refrigeration technicians to better determine where and how the issue is happening. Below is a remote monitoring station with a thermistor probe.
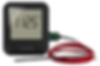
Below are graphs that were collected during an investigation into a refrigerated case that was sporadically not holding temp. There was a remote station monitoring the box temperature and another that was monitoring the evaporator coil.

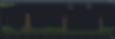
If you need a monitoring system to make sure that you do not lose product, give us a call. Call 512-651-4565 in Austin and Lubbock, Texas (806) 787-4985 Or Visit our website at www.tripointrefrigeration.com